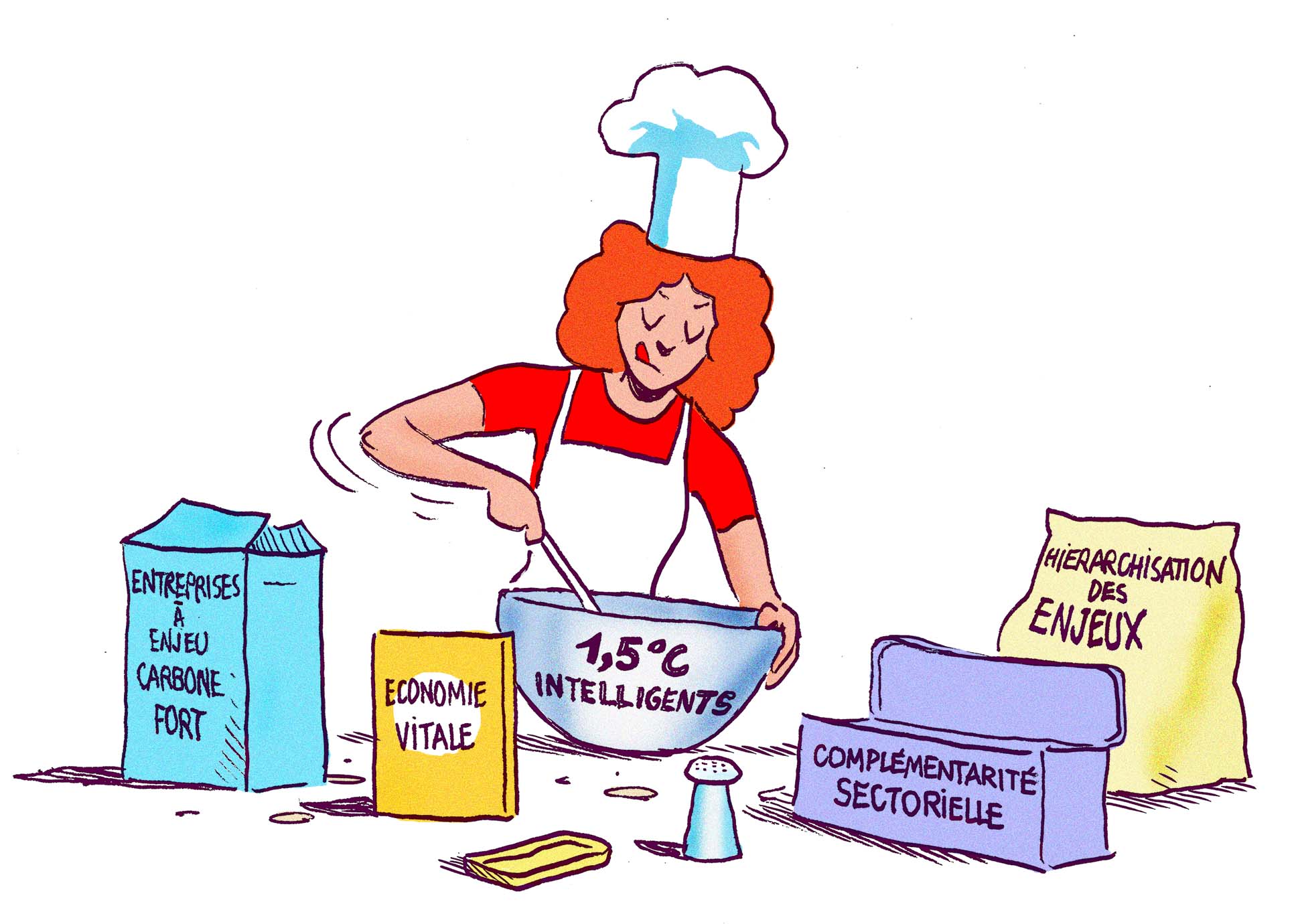
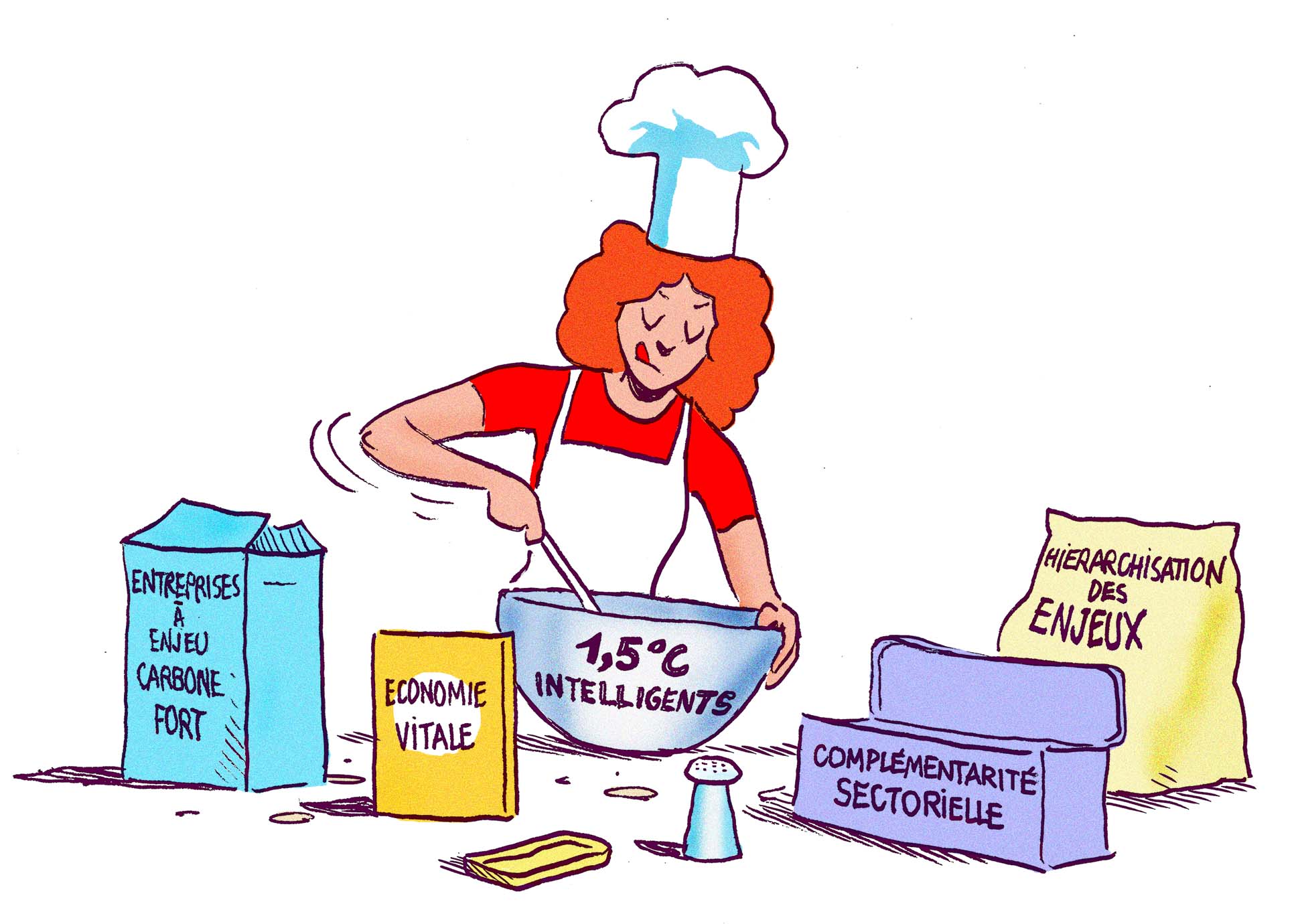
26 juin 2023
Quand vous jetez votre téléphone portable à la poubelle, il a une grande chance de finir fondu par Boliden. Chaque jour, sa fonderie de Rönnskär, située dans le nord de la Suède, accueille plusieurs trains et camions remplis de centaines de tonnes de déchets électroniques. Dans ces déchets, figurent des circuits imprimés d’ordinateurs et des téléphones portables provenant d’Europe. Une fois récupérés et recyclés, ces résidus de cuivre sont introduits dans son circuit de production, pour fabriquer du Recycled Copper, soit des produits de cuivre à partir de cuivre récupéré dans des déchets électroniques.
Aujourd’hui, Boliden est capable de recycler 120 000 tonnes de matériaux par an, ce qui la place en première position mondiale du recyclage de l’électronique.
Au cours des 25 prochaines années, nous aurons besoin de la même quantité de cuivre que celle que l’humanité a produite au cours des 500 dernières années. La demande pour ce métal est colossale : bien supérieure aux capacités des mines et des fonderies actuelles, détaille dans son rapport l’International Copper Study Group, groupe de recherche réunissant 39 pays producteurs, consommateurs et revendeurs de cuivre. 2022 a d’ailleurs été une année record pour la demande de cuivre : 32,1 Mt sur le marché selon le rapport annuel de l’International Copper Study Group, groupe d’étude sur ce métal.
La transition écologique, qui est devenue une nécessité, passe par la fabrication de produits qui respectent mieux la planète et génèrent peu voire pas du tout de gaz à effets de serre. Mais ces technologies utilisent majoritairement des matières premières en tension : des métaux rares tels que le cuivre et le lithium. Et pour développer les énergies renouvelables tels que les parcs éoliens et les champs de panneaux solaires, la demande en métaux rares est exponentielle. Par exemple, chaque éolienne contient entre 2.5 et 6.4 tonnes de cuivre dans ses trois pales, son générateur, son câblage et son transformateur.
Aujourd’hui, les sources de cuivre sont pour l’instant obligatoirement à l’étranger. Le Chili, premier pays exploitant de mines de cuivre, ne dispose pas de fonderies modernes qui peuvent répondre à la demande de cuivre et doit donc exporter le minerai pour le faire fondre.
La Chine, leader de la production de cuivre avec 30 000 kilos tonnes de cuivre fondu par an, prévoit d’ouvrir de nouvelles mines et fonderies d’ici 2025. Mais jusque-là, une part importante de la demande en cuivre n’est pas adressée : la transition écologique se voit ainsi retardée faute de ressources naturelles disponibles immédiatement. Augmenter la capacité d’extraction des mines et de production des fonderies n’est pas réalisable à court terme.
Et troisième difficulté : les pays producteurs de cuivre voient le taux de concentration de cuivre des gisements actuels baisser continuellement. L’extraction du cuivre doit être de plus en plus profonde et coûteuse pour obtenir un minerai utilisable industriellement.
Parce que les besoins en cuivre peuvent être source de tensions économiques et géopolitiques, l’Union Européenne a décidé début 2023 d’un plan d’action pour garantir les approvisionnements en métaux critiques ou métaux rares. Aujourd’hui dans l’UE, 50 % du cuivre utilisé industriellement provient du recyclage.
“D’ici 2030, les besoins de terres rares pour produire des turbines éoliennes vont être multipliés par cinq, ceux du lithium, indispensable pour produire des batteries pour véhicules électriques, vont être multipliés par 12 puis par 21 d’ici 2050” affirme Valdis Dombrovskis, vice-président de la Commission Européenne, lors de la présentation de la Loi sur les matières premières critiques (Critical Raw Materials Act) en mars 2023.
L’Union veut renforcer la filière de recyclage entre ses pays membres pour réutiliser les matériaux récupérés dans la production de nouveaux objets nécessaires à la transition énergétique.
La filière du recyclage du cuivre est une priorité car elle réduit l’impact environnemental de sa production. Le cuivre peut être entièrement recyclé et réutilisé à l’infini, sans perte de performance. C’est tout ce qu’a compris le groupe suédois Boliden en développant depuis plusieurs années la production de cuivre décarboné, à partir de déchets électroniques.
En 2023, il faut compter 50 semaines d’attente pour raccorder un parc éolien offshore au réseau électrique à cause d’une pénurie de câbles en cuivre. Les acteurs du cuivre ont bien compris l’importance de ce métal stratégique et organisent depuis plusieurs années sa récupération et son recyclage.
Depuis les années 1960, Boliden œuvre au recyclage de déchets. Ses deux fonderies de Rönnskär et Bergsöe, situées au nord et au sud de la Suède, traitent 4 millions de batteries électroniques de voiture par an, et deux millions de smartphones par jour. Ces déchets électroniques sont une source de métaux précieux : or et argent, et de métaux de base, tels que le cuivre.
Une fois que les déchets sont arrivés dans l’usine, ils sont nettoyés au maximum du fer et de l’aluminium qu’ils contiennent puis passent à l’échantillonnage. Cette étape permet d’évaluer leur teneur en métaux rares avant que chaque déchet soit envoyé sur la chaîne de traitement. Les circuits imprimés livrés entiers sont écrasés par un broyeur. Les autres déchets sont chauffés puis mélangés au reste des matériaux à traiter pour ensuite arriver à l’étape de fusion.
La technologie de recyclage du cuivre notamment employée par Boliden est celle dite de Kaldo. Boliden a spécialement adapté un four Kaldo à la fusion du matériel électronique : ce four traditionnel de fusion était jusque-là utilisé uniquement pour la fonte de minerais ou de concentré de minerais. Boliden l’exploite pour récupérer le cuivre contenu dans les déchets traités. Ce four Kaldo n’a pas besoin d’énergie extérieure : le plastique contenu dans la matière première fournit suffisamment d’énergie à la fusion.
Grâce à cette innovation dans la récupération du cuivre contenu dans les déchets électroniques, le groupe a produit 218 kilotonnes de cuivre en 2022. Elle est la première entreprise mondiale à produire du cuivre bas carbone : elle l’a appelé Low-Carbon Copper, et le fabrique à partir de concentrés provenant de ses propres mines de cuivre et de cuivre récupéré parmi les déchets électroniques.
Boliden poursuit une stratégie de production de cuivre à bas carbone qui vise à atteindre les objectifs des accords de Paris en matière d’émission de gaz à effet de serre et de respect de l’environnement. La part de cuivre produit issu du recyclage augmente d’année après année. Le groupe suédois mène également une bonne mutualisation des transports de marchandises : chaque jour, un train part de la fonderie avec du cuivre prêt à être utilisé et le même train revient ensuite chargé de déchets électroniques.
Parmi les sujets d’avenir figure le recyclage des éoliennes arrivées en fin de vie, aussi bien sur terre qu’ en mer. Boliden estime que 95% du cuivre contenu dans les parcs éoliens terrestres peut être recyclé et réintroduit dans la production de cuivre.
Mais recycler les éoliennes offshore soulève une problématique environnementale qui se révèle difficile à oublier quand on veut respecter les Accords de Paris. Effectivement, se pose la question de la protection des fonds marins lors des opérations de récupération des câbles sous-marins qui contiennent d’importantes quantités de cuivre. La filière recyclage doit prendre en compte ces paramètres, sachant qu’aucune réglementation européenne ou mondiale n’existe à ce jour.
En France, un acteur du recyclage tire également son épingle du jeu : WeeeCycling. La société normande opère depuis 2019 dans le traitement des déchets électroniques. Grâce à ses procédés innovants, elle utilise 40 litres d’eau pour produire 1 kilo de métal issu du recyclage de déchets électroniques contre 2 millions de litres d’eau pour la production classique de métal chez les autres acteurs du marché. Chaque année, les 10 000 tonnes de déchets collectées permettent à WeeeCycling d’extraire 400 tonnes d’or, d’argent, de cuivre et platinoïdes.
Les pouvoirs publics français se sont saisis du sujet de la pénurie des métaux rares. Le plan France 2030, présenté fin 2022, finance le soutien aux acteurs du recyclage de déchets électroniques tels que WeeeCycling. 1 milliard d’euros va servir à faire émerger de nouvelles usines de recyclage et de production de ces métaux critiques et matériaux. L’objectif : rendre possible la transition écologique qui a gourmande en métaux rares. Grâce au soutien public, la capacité de production de métaux critiques du site de WEEECycling à Tourville les Ifs va être multipliée par 10.
La filière du recyclage a de beaux jours devant elle sachant que chaque année notre planète produit 50 millions de tonnes de déchets électroniques !
26 juin 2023
Quand vous jetez votre téléphone portable à la poubelle, il a une grande chance de finir fondu par Boliden. Chaque jour, sa fonderie de Rönnskär, située dans le nord de la Suède, accueille plusieurs trains et camions remplis de centaines de tonnes de déchets électroniques. Dans ces déchets, figurent des circuits imprimés d’ordinateurs et des téléphones portables provenant d’Europe. Une fois récupérés et recyclés, ces résidus de cuivre sont introduits dans son circuit de production, pour fabriquer du Recycled Copper, soit des produits de cuivre à partir de cuivre récupéré dans des déchets électroniques.
Aujourd’hui, Boliden est capable de recycler 120 000 tonnes de matériaux par an, ce qui la place en première position mondiale du recyclage de l’électronique.
Au cours des 25 prochaines années, nous aurons besoin de la même quantité de cuivre que celle que l’humanité a produite au cours des 500 dernières années. La demande pour ce métal est colossale : bien supérieure aux capacités des mines et des fonderies actuelles, détaille dans son rapport l’International Copper Study Group, groupe de recherche réunissant 39 pays producteurs, consommateurs et revendeurs de cuivre. 2022 a d’ailleurs été une année record pour la demande de cuivre : 32,1 Mt sur le marché selon le rapport annuel de l’International Copper Study Group, groupe d’étude sur ce métal.
La transition écologique, qui est devenue une nécessité, passe par la fabrication de produits qui respectent mieux la planète et génèrent peu voire pas du tout de gaz à effets de serre. Mais ces technologies utilisent majoritairement des matières premières en tension : des métaux rares tels que le cuivre et le lithium. Et pour développer les énergies renouvelables tels que les parcs éoliens et les champs de panneaux solaires, la demande en métaux rares est exponentielle. Par exemple, chaque éolienne contient entre 2.5 et 6.4 tonnes de cuivre dans ses trois pales, son générateur, son câblage et son transformateur.
Aujourd’hui, les sources de cuivre sont pour l’instant obligatoirement à l’étranger. Le Chili, premier pays exploitant de mines de cuivre, ne dispose pas de fonderies modernes qui peuvent répondre à la demande de cuivre et doit donc exporter le minerai pour le faire fondre.
La Chine, leader de la production de cuivre avec 30 000 kilos tonnes de cuivre fondu par an, prévoit d’ouvrir de nouvelles mines et fonderies d’ici 2025. Mais jusque-là, une part importante de la demande en cuivre n’est pas adressée : la transition écologique se voit ainsi retardée faute de ressources naturelles disponibles immédiatement. Augmenter la capacité d’extraction des mines et de production des fonderies n’est pas réalisable à court terme.
Et troisième difficulté : les pays producteurs de cuivre voient le taux de concentration de cuivre des gisements actuels baisser continuellement. L’extraction du cuivre doit être de plus en plus profonde et coûteuse pour obtenir un minerai utilisable industriellement.
Parce que les besoins en cuivre peuvent être source de tensions économiques et géopolitiques, l’Union Européenne a décidé début 2023 d’un plan d’action pour garantir les approvisionnements en métaux critiques ou métaux rares. Aujourd’hui dans l’UE, 50 % du cuivre utilisé industriellement provient du recyclage.
“D’ici 2030, les besoins de terres rares pour produire des turbines éoliennes vont être multipliés par cinq, ceux du lithium, indispensable pour produire des batteries pour véhicules électriques, vont être multipliés par 12 puis par 21 d’ici 2050” affirme Valdis Dombrovskis, vice-président de la Commission Européenne, lors de la présentation de la Loi sur les matières premières critiques (Critical Raw Materials Act) en mars 2023.
L’Union veut renforcer la filière de recyclage entre ses pays membres pour réutiliser les matériaux récupérés dans la production de nouveaux objets nécessaires à la transition énergétique.
La filière du recyclage du cuivre est une priorité car elle réduit l’impact environnemental de sa production. Le cuivre peut être entièrement recyclé et réutilisé à l’infini, sans perte de performance. C’est tout ce qu’a compris le groupe suédois Boliden en développant depuis plusieurs années la production de cuivre décarboné, à partir de déchets électroniques.
En 2023, il faut compter 50 semaines d’attente pour raccorder un parc éolien offshore au réseau électrique à cause d’une pénurie de câbles en cuivre. Les acteurs du cuivre ont bien compris l’importance de ce métal stratégique et organisent depuis plusieurs années sa récupération et son recyclage.
Depuis les années 1960, Boliden œuvre au recyclage de déchets. Ses deux fonderies de Rönnskär et Bergsöe, situées au nord et au sud de la Suède, traitent 4 millions de batteries électroniques de voiture par an, et deux millions de smartphones par jour. Ces déchets électroniques sont une source de métaux précieux : or et argent, et de métaux de base, tels que le cuivre.
Une fois que les déchets sont arrivés dans l’usine, ils sont nettoyés au maximum du fer et de l’aluminium qu’ils contiennent puis passent à l’échantillonnage. Cette étape permet d’évaluer leur teneur en métaux rares avant que chaque déchet soit envoyé sur la chaîne de traitement. Les circuits imprimés livrés entiers sont écrasés par un broyeur. Les autres déchets sont chauffés puis mélangés au reste des matériaux à traiter pour ensuite arriver à l’étape de fusion.
La technologie de recyclage du cuivre notamment employée par Boliden est celle dite de Kaldo. Boliden a spécialement adapté un four Kaldo à la fusion du matériel électronique : ce four traditionnel de fusion était jusque-là utilisé uniquement pour la fonte de minerais ou de concentré de minerais. Boliden l’exploite pour récupérer le cuivre contenu dans les déchets traités. Ce four Kaldo n’a pas besoin d’énergie extérieure : le plastique contenu dans la matière première fournit suffisamment d’énergie à la fusion.
Grâce à cette innovation dans la récupération du cuivre contenu dans les déchets électroniques, le groupe a produit 218 kilotonnes de cuivre en 2022. Elle est la première entreprise mondiale à produire du cuivre bas carbone : elle l’a appelé Low-Carbon Copper, et le fabrique à partir de concentrés provenant de ses propres mines de cuivre et de cuivre récupéré parmi les déchets électroniques.
Boliden poursuit une stratégie de production de cuivre à bas carbone qui vise à atteindre les objectifs des accords de Paris en matière d’émission de gaz à effet de serre et de respect de l’environnement. La part de cuivre produit issu du recyclage augmente d’année après année. Le groupe suédois mène également une bonne mutualisation des transports de marchandises : chaque jour, un train part de la fonderie avec du cuivre prêt à être utilisé et le même train revient ensuite chargé de déchets électroniques.
Parmi les sujets d’avenir figure le recyclage des éoliennes arrivées en fin de vie, aussi bien sur terre qu’ en mer. Boliden estime que 95% du cuivre contenu dans les parcs éoliens terrestres peut être recyclé et réintroduit dans la production de cuivre.
Mais recycler les éoliennes offshore soulève une problématique environnementale qui se révèle difficile à oublier quand on veut respecter les Accords de Paris. Effectivement, se pose la question de la protection des fonds marins lors des opérations de récupération des câbles sous-marins qui contiennent d’importantes quantités de cuivre. La filière recyclage doit prendre en compte ces paramètres, sachant qu’aucune réglementation européenne ou mondiale n’existe à ce jour.
En France, un acteur du recyclage tire également son épingle du jeu : WeeeCycling. La société normande opère depuis 2019 dans le traitement des déchets électroniques. Grâce à ses procédés innovants, elle utilise 40 litres d’eau pour produire 1 kilo de métal issu du recyclage de déchets électroniques contre 2 millions de litres d’eau pour la production classique de métal chez les autres acteurs du marché. Chaque année, les 10 000 tonnes de déchets collectées permettent à WeeeCycling d’extraire 400 tonnes d’or, d’argent, de cuivre et platinoïdes.
Les pouvoirs publics français se sont saisis du sujet de la pénurie des métaux rares. Le plan France 2030, présenté fin 2022, finance le soutien aux acteurs du recyclage de déchets électroniques tels que WeeeCycling. 1 milliard d’euros va servir à faire émerger de nouvelles usines de recyclage et de production de ces métaux critiques et matériaux. L’objectif : rendre possible la transition écologique qui a gourmande en métaux rares. Grâce au soutien public, la capacité de production de métaux critiques du site de WEEECycling à Tourville les Ifs va être multipliée par 10.
La filière du recyclage a de beaux jours devant elle sachant que chaque année notre planète produit 50 millions de tonnes de déchets électroniques !
26 juin 2023
Quand vous jetez votre téléphone portable à la poubelle, il a une grande chance de finir fondu par Boliden. Chaque jour, sa fonderie de Rönnskär, située dans le nord de la Suède, accueille plusieurs trains et camions remplis de centaines de tonnes de déchets électroniques. Dans ces déchets, figurent des circuits imprimés d’ordinateurs et des téléphones portables provenant d’Europe. Une fois récupérés et recyclés, ces résidus de cuivre sont introduits dans son circuit de production, pour fabriquer du Recycled Copper, soit des produits de cuivre à partir de cuivre récupéré dans des déchets électroniques.
Aujourd’hui, Boliden est capable de recycler 120 000 tonnes de matériaux par an, ce qui la place en première position mondiale du recyclage de l’électronique.
Au cours des 25 prochaines années, nous aurons besoin de la même quantité de cuivre que celle que l’humanité a produite au cours des 500 dernières années. La demande pour ce métal est colossale : bien supérieure aux capacités des mines et des fonderies actuelles, détaille dans son rapport l’International Copper Study Group, groupe de recherche réunissant 39 pays producteurs, consommateurs et revendeurs de cuivre. 2022 a d’ailleurs été une année record pour la demande de cuivre : 32,1 Mt sur le marché selon le rapport annuel de l’International Copper Study Group, groupe d’étude sur ce métal.
La transition écologique, qui est devenue une nécessité, passe par la fabrication de produits qui respectent mieux la planète et génèrent peu voire pas du tout de gaz à effets de serre. Mais ces technologies utilisent majoritairement des matières premières en tension : des métaux rares tels que le cuivre et le lithium. Et pour développer les énergies renouvelables tels que les parcs éoliens et les champs de panneaux solaires, la demande en métaux rares est exponentielle. Par exemple, chaque éolienne contient entre 2.5 et 6.4 tonnes de cuivre dans ses trois pales, son générateur, son câblage et son transformateur.
Aujourd’hui, les sources de cuivre sont pour l’instant obligatoirement à l’étranger. Le Chili, premier pays exploitant de mines de cuivre, ne dispose pas de fonderies modernes qui peuvent répondre à la demande de cuivre et doit donc exporter le minerai pour le faire fondre.
La Chine, leader de la production de cuivre avec 30 000 kilos tonnes de cuivre fondu par an, prévoit d’ouvrir de nouvelles mines et fonderies d’ici 2025. Mais jusque-là, une part importante de la demande en cuivre n’est pas adressée : la transition écologique se voit ainsi retardée faute de ressources naturelles disponibles immédiatement. Augmenter la capacité d’extraction des mines et de production des fonderies n’est pas réalisable à court terme.
Et troisième difficulté : les pays producteurs de cuivre voient le taux de concentration de cuivre des gisements actuels baisser continuellement. L’extraction du cuivre doit être de plus en plus profonde et coûteuse pour obtenir un minerai utilisable industriellement.
Parce que les besoins en cuivre peuvent être source de tensions économiques et géopolitiques, l’Union Européenne a décidé début 2023 d’un plan d’action pour garantir les approvisionnements en métaux critiques ou métaux rares. Aujourd’hui dans l’UE, 50 % du cuivre utilisé industriellement provient du recyclage.
“D’ici 2030, les besoins de terres rares pour produire des turbines éoliennes vont être multipliés par cinq, ceux du lithium, indispensable pour produire des batteries pour véhicules électriques, vont être multipliés par 12 puis par 21 d’ici 2050” affirme Valdis Dombrovskis, vice-président de la Commission Européenne, lors de la présentation de la Loi sur les matières premières critiques (Critical Raw Materials Act) en mars 2023.
L’Union veut renforcer la filière de recyclage entre ses pays membres pour réutiliser les matériaux récupérés dans la production de nouveaux objets nécessaires à la transition énergétique.
La filière du recyclage du cuivre est une priorité car elle réduit l’impact environnemental de sa production. Le cuivre peut être entièrement recyclé et réutilisé à l’infini, sans perte de performance. C’est tout ce qu’a compris le groupe suédois Boliden en développant depuis plusieurs années la production de cuivre décarboné, à partir de déchets électroniques.
En 2023, il faut compter 50 semaines d’attente pour raccorder un parc éolien offshore au réseau électrique à cause d’une pénurie de câbles en cuivre. Les acteurs du cuivre ont bien compris l’importance de ce métal stratégique et organisent depuis plusieurs années sa récupération et son recyclage.
Depuis les années 1960, Boliden œuvre au recyclage de déchets. Ses deux fonderies de Rönnskär et Bergsöe, situées au nord et au sud de la Suède, traitent 4 millions de batteries électroniques de voiture par an, et deux millions de smartphones par jour. Ces déchets électroniques sont une source de métaux précieux : or et argent, et de métaux de base, tels que le cuivre.
Une fois que les déchets sont arrivés dans l’usine, ils sont nettoyés au maximum du fer et de l’aluminium qu’ils contiennent puis passent à l’échantillonnage. Cette étape permet d’évaluer leur teneur en métaux rares avant que chaque déchet soit envoyé sur la chaîne de traitement. Les circuits imprimés livrés entiers sont écrasés par un broyeur. Les autres déchets sont chauffés puis mélangés au reste des matériaux à traiter pour ensuite arriver à l’étape de fusion.
La technologie de recyclage du cuivre notamment employée par Boliden est celle dite de Kaldo. Boliden a spécialement adapté un four Kaldo à la fusion du matériel électronique : ce four traditionnel de fusion était jusque-là utilisé uniquement pour la fonte de minerais ou de concentré de minerais. Boliden l’exploite pour récupérer le cuivre contenu dans les déchets traités. Ce four Kaldo n’a pas besoin d’énergie extérieure : le plastique contenu dans la matière première fournit suffisamment d’énergie à la fusion.
Grâce à cette innovation dans la récupération du cuivre contenu dans les déchets électroniques, le groupe a produit 218 kilotonnes de cuivre en 2022. Elle est la première entreprise mondiale à produire du cuivre bas carbone : elle l’a appelé Low-Carbon Copper, et le fabrique à partir de concentrés provenant de ses propres mines de cuivre et de cuivre récupéré parmi les déchets électroniques.
Boliden poursuit une stratégie de production de cuivre à bas carbone qui vise à atteindre les objectifs des accords de Paris en matière d’émission de gaz à effet de serre et de respect de l’environnement. La part de cuivre produit issu du recyclage augmente d’année après année. Le groupe suédois mène également une bonne mutualisation des transports de marchandises : chaque jour, un train part de la fonderie avec du cuivre prêt à être utilisé et le même train revient ensuite chargé de déchets électroniques.
Parmi les sujets d’avenir figure le recyclage des éoliennes arrivées en fin de vie, aussi bien sur terre qu’ en mer. Boliden estime que 95% du cuivre contenu dans les parcs éoliens terrestres peut être recyclé et réintroduit dans la production de cuivre.
Mais recycler les éoliennes offshore soulève une problématique environnementale qui se révèle difficile à oublier quand on veut respecter les Accords de Paris. Effectivement, se pose la question de la protection des fonds marins lors des opérations de récupération des câbles sous-marins qui contiennent d’importantes quantités de cuivre. La filière recyclage doit prendre en compte ces paramètres, sachant qu’aucune réglementation européenne ou mondiale n’existe à ce jour.
En France, un acteur du recyclage tire également son épingle du jeu : WeeeCycling. La société normande opère depuis 2019 dans le traitement des déchets électroniques. Grâce à ses procédés innovants, elle utilise 40 litres d’eau pour produire 1 kilo de métal issu du recyclage de déchets électroniques contre 2 millions de litres d’eau pour la production classique de métal chez les autres acteurs du marché. Chaque année, les 10 000 tonnes de déchets collectées permettent à WeeeCycling d’extraire 400 tonnes d’or, d’argent, de cuivre et platinoïdes.
Les pouvoirs publics français se sont saisis du sujet de la pénurie des métaux rares. Le plan France 2030, présenté fin 2022, finance le soutien aux acteurs du recyclage de déchets électroniques tels que WeeeCycling. 1 milliard d’euros va servir à faire émerger de nouvelles usines de recyclage et de production de ces métaux critiques et matériaux. L’objectif : rendre possible la transition écologique qui a gourmande en métaux rares. Grâce au soutien public, la capacité de production de métaux critiques du site de WEEECycling à Tourville les Ifs va être multipliée par 10.
La filière du recyclage a de beaux jours devant elle sachant que chaque année notre planète produit 50 millions de tonnes de déchets électroniques !
Chloé a concocté pour vous une recette financière bas carbone robuste et adaptée à vous
Avec votre investissement Chloé, acquérez des informations sur les défis technico-industriels actuels et à venir.
Découvrez les débats en cours et apportez votre expertise !
Avec votre investissement Chloé, acquérez des informations sur les défis technico-industriels actuels et à venir.
Découvrez les débats en cours et apportez votre expertise !
Navigation
À propos
À propos
Chloé in the sky
Siège social : 2 rue Albert Rolland 29200 Brest – Établissement secondaire : 29 rue de Choiseul 75002 Paris
Téléphone : 01 83 64 27 38
SAS au capital de 177 400 € immatriculée à Paris
RCS : 899173629
Chloé in the sky est une Société par Action Simplifiée
(SAS) immatriculée à l’ORIAS au numéro 21005578 en date du 25/06/2021 en tant que Conseiller en Investissement Financier (CIF) et courtier en assurance (COA).
Navigation
À propos
À propos
Chloé in the sky
Siège social : 2 rue Albert Rolland 29200 Brest – Établissement secondaire : 29 rue de Choiseul 75002 Paris
Téléphone : 01 83 64 27 38
SAS au capital de 110 000 € immatriculée à Paris
RCS : 899173629
Chloé in the sky est une Société par Action Simplifiée
(SAS) immatriculée à l’ORIAS au numéro 21005578 en date du 25/06/2021 en tant que Conseiller en Investissement Financier (CIF) et courtier en assurance (COA).
Navigation
À propos
À propos
Chloé in the sky
Siège social : 2 rue Albert Rolland 29200 Brest – Établissement secondaire : 29 rue de Choiseul 75002 Paris
Téléphone : 01 83 64 27 38
SAS au capital de 110 000 € immatriculée à Paris
RCS : 899173629
Chloé in the sky est une Société par Action Simplifiée
(SAS) immatriculée à l’ORIAS au numéro 21005578 en date du 25/06/2021 en tant que Conseiller en Investissement Financier (CIF) et courtier en assurance (COA).
© Chloé in the sky . Tous droits réservés.
Vous souhaitez
en savoir plus ?
Nous vous contactons dans les 48h pour un échange autour de votre projet.
Acquérez des informations
sur les défis technico-industriels
actuels et à venir.